Ligne de production de ciment 3000tpd
Le projet de ligne de production de ciment EPC de Pengfei comprend des services tels que la conception du processus, la fourniture d’équipements (y compris les pièces mécaniques et électriques), le génie civil, l’installation et la mise en service, l’exploitation d’essai, l’atteinte des normes de production et la livraison finale. Les équipements mécaniques comprennent le concassage et le transport du calcaire, le concassage de l’argile et le parc de pré-homogénéisation des matières premières auxiliaires, la station de dosage des matières premières, le broyage des matières premières et le traitement des gaz résiduaires, l’entrepôt d’homogénéisation des matières premières et les matières premières entrant dans le four et la queue du four de cuisson, le four de cuisson et le conduit d’air tertiaire, la tête du four de cuisson, le transport de clinker, le clinker.
Introduction
Le projet de ligne de production de ciment EPC de Pengfei comprend des services tels que la conception du processus, la fourniture d’équipements (y compris les pièces mécaniques et électriques), le génie civil, l’installation et la mise en service, l’exploitation d’essai, l’atteinte des normes de production et la livraison finale. Les équipements mécaniques comprennent le concassage et le transport du calcaire, le concassage de l’argile et le parc de pré-homogénéisation des matières premières auxiliaires, la station de dosage des matières premières, le broyage des matières premières et le traitement des gaz résiduaires, l’entrepôt d’homogénéisation des matières premières et la queue du four de cuisson, le four de cuisson et le conduit d’air tertiaire, la tête du four de cuisson, le transport de clinker, le stockage et le transport de clinker, la station de dosage de ciment et le vrac de clinker, gypse, concassage et transport de matériaux mixtes, broyage et transport de ciment, stockage et transport de ciment, emballage de ciment, chargement de ciment en sac, vrac automobile de ciment, atelier de réparation de machines et entrepôt de matériaux de somme.Paramètres du processus
(1) Sortie de clinker : ≥3000 t / j ; (2) Consommation de chaleur pour la combustion du clinker (3) Consommation d’énergie complète pour le clinker (4) Consommation d’énergie complète pour le ciment (5) Intensité du clinker sur 28 jours (6) Concentration des émissions de poussièresMéthode de production
La production de ciment utilise du calcaire et de l’argile comme principales matières premières. Après le broyage et le dosage, des matières premières sont produites. Les matières premières sont introduites dans un four rotatif à ciment pour la calcination. Ensuite, le clinker est ajouté avec une quantité appropriée de gypse, mélangé à des matériaux mélangés ou à des additifs, et broyé par du ciment. Les équipements de production de ciment utilisent généralement le processus de production de ciment sec. Méthode permettant de sécher simultanément des matières premières et de les broyer en poudre de farine crue, puis de les introduire dans un four rotatif sec pour la calcination de matériaux matures. Le principal avantage de la production à sec est la faible consommation de chaleur. |
Description du déroulement du processus
5.1 Concasseur de calcaireUne installation de concassage de calcaire est installée dans l’usine. Le calcaire extrait est déversé par camions dans une trémie basculante en béton et revêtue de plaques d’acier avec des barres et extraite au moyen d’un alimentateur à tablier robuste d’une capacité de 550 t/h vers le concasseur.
Le concasseur est un concasseur à marteaux d’une capacité de 550 t/h. Il est capable de broyer des morceaux de calcaire d’une taille maximale de 1 000 mm d’un bord à l’autre jusqu’à une taille inférieure à 75 mm. Pour éviter que le concasseur ne soit surchargé, la vitesse de l’alimentateur sur tablier est modifiée par une unité d’entraînement hydraulique en réponse à la consommation d’énergie du moteur d’entraînement du concasseur. Un convoyeur à raclettes est équipé de manière à ce que les matériaux déversés de l’alimentateur à tablier y soient collectés. Le calcaire concassé est transporté par des convoyeurs à bande vers un lit de pré-mélange circulaire. Une peseuse à bande avec totalisateur est fournie pour la mesure d’une capacité de broyage. Un filtre à manches de type balayage à jet d’impulsion est fourni pour le dépoussiérage de l’installation de broyage.
5.2 Pré-homogénéisation du calcaireLe calcaire concassé est empilé d’une capacité de 600 t/h sur un stock circulaire de 24 000 tonnes. Un récupérateur de type pont d’une capacité de 300 t/h est prévu pour l’extraction du calcaire sur un convoyeur à bande ultérieur
5.3 Concassage et transport des matériaux auxiliaires et du charbonLe correctif (argile, minerai de fer, etc.) et le charbon seront transportés à l’usine par camion à benne basculante. Le concasseur sera fixé dans un stock couvert. Un alimentateur à tablier alimentera les matériaux avec une teneur en humidité inférieure à 10 dans un concasseur. Les matériaux broyés seront transportés à l’aide d’un convoyeur à bande jusqu’à un long parc de stockage de pré-mélange.
5.4 Correction et prémélange du charbon Les correcteurs sont déversés par camions dans une trémie basculante en béton et revêtue de plaques d’acier avec des barres et extraites au moyen d’un tablier d’alimentation à usage intensif vers le concasseur.
Les matériaux broyés seront stockés dans un lit de prémélange longitudinal. Une peseuse à bande avec totalisateur est fournie pour la mesure d’une capacité de broyage.
Le charbon est acheminé vers le stockage de prémélange à l’aide d’un convoyeur à bande. Ces matériaux sont empilés par une flèche latérale de type rampe, formant deux stocks longitudinaux. Deux récupérateurs de type cantilever sont prévus pour l’extraction du matériau correcteur sur un convoyeur à bande ultérieur vers la trémie de proportion de matières premières et la trémie à charbon.
5.5 Dosage et transport des matières premièresLa station de dosage des matières premières dispose de 4 bacs : le bac à calcaire, le bac à mélange, le bac à argile, le bac à fer. Sous chaque bac, un alimentateur de pesée décharge automatiquement et en douceur le matériau du bac selon un rapport de dosage donné. La matière première mélangée est transportée vers l’usine par un convoyeur à bande.
5.6 Broyage des matières premières et traitement des gaz résiduaires Un broyeur vertical sera utilisé pour le broyage des matières premières. La capacité du broyeur de matières premières est de 210t/h. Les matières premières seront proportionnées selon le rapport défini avant d’être acheminées vers le moulin pour le broyage et le séchage. Le matériau broyé sera transporté par voie aérienne vers le séparateur cyclonique et les particules grossières seront collectées par le séparateur intégré et renvoyées au broyeur pour être rebroyées. L’air chargé de poussière qui s’échappe du séparateur cyclonique sera traité dans un filtre à manches avant d’être émis dans l’atmosphère (<30mg/Nm3). The raw meal collected by the cyclone separator and the bag filter will be sent to the raw meal homogenizing silo. The hot air for drying the raw material will be drawn from the cyclone preheater.
5.7 Silo d’homogénéisation de farine crue
Le système de mélange comprend des systèmes d’alimentation multiples et un silo de mélange continu d’une capacité de 7 500 tonnes. Le système d’alimentation multiple garantit la formation de couches uniformes sur toute la section transversale du silo. L’action d’homogénéisation est effectuée par l’écoulement de l’entonnoir pendant le processus de déchargement activé par l’aération cyclique dans la zone inférieure. Ce système de mélange présente une efficacité d’homogénéisation élevée avec une faible consommation d’énergie. La farine crue homogénéisée est envoyée au système d’alimentation du four dans l’espace inférieur du silo de mélange.
La farine crue homogénéisée est dosée par une soupape de débit électrique et un doseur de pesée à bande, après quoi elle est envoyée par un équipement de transport et un élévateur à godets vers le conduit en amont du préchauffeur. L’air du silo d’homogénéisation doit être fourni par des souffleurs de racines.
5.8 Système d’alimentation du four
La farine crue du silo d’homogénéisation de la farine crue est envoyée dans un bac de pesée. Après avoir été dosée par un débitmètre à impact sous le bac, la farine crue est envoyée au système de préchauffage par un élévateur à godets à bande. Lorsque le four est arrêté temporairement, la farine crue est renvoyée dans le silo d’homogénéisation de la farine crue.
5.9 Système de frittage de clinker
Un four rotatif à sec Φ4.0x60m avec une série unique, un préchauffeur et un précalcinateur à cyclone à 5 étages ainsi qu’un refroidisseur à grille seront utilisés. La capacité du système est de 2 500 t/j et la consommation de chaleur de 740 kcal/kg. La farine crue sera pesée avant d’être introduite dans le préchauffeur pour le préchauffage et la décarbonatation partielle, puis dans le précalcinateur pour la calcination. Le taux de décarbonatation du CaCO3 dans la farine crue à l’entrée du four est d’environ 95 %. La farine crue est ensuite décarbonée et brûlée dans le four. Le clinker dont la température dépasse 1 350 °C entrera dans le refroidisseur de grille pour la trempe. La température du clinker à la sortie du refroidisseur sera de 65°C plus la température ambiante.
Les gaz d’échappement du préchauffeur dont la température est d’environ 310°C seront utilisés pour le séchage des matières premières. Les gaz d’échappement sortant du refroidisseur seront introduits dans le filtre à manches pour la purification avant d’être émis.
5.10 Stockage du clinker
À partir du refroidisseur, le clinker est déchargé sur un convoyeur à chaîne à godets de clinker et transporté vers un silo à clinker de 27 000 tonnes. Un bac à clinker sous-brûlé d’une capacité de 500 tonnes sera installé à l’intérieur du silo. Le clinker sera transporté vers le bac de dosage du clinker par des convoyeurs à bande.
5.11 Concassage et convoyage du gypse et des matériaux additifs
Transporté par camion sur le site depuis sa mine, le gypse est directement déchargé à une bascule exclusive et concassé dans le concasseur PEX250×1000. Lorsque le concasseur est éteint, le gypse est conservé en tas exclusif, puis envoyé à la benne de broyage par le chargeur frontal. Après le broyage, le gypse est ensuite envoyé vers le silo par lots par des convoyeurs à bande.
5.12 Broyage du ciment
Le clinker, le gypse, le calcaire ou tout autre additif sont extraits de la trémie respective au moyen d’alimentateurs de pesée équipés d’un régulateur de vitesse proportionnellement à une cadence prédéterminée.
Deux unités de broyeurs à boulets φ3,8×13m sont l’équipement principal du département de broyage du ciment. Les alimentateurs de pesée sous les bacs alimenteront les matériaux selon le rapport de réglage. Le mélange sera acheminé vers le moulin par le convoyeur à bande. Le matériau de ciment broyé sera envoyé au séparateur par l’élévateur à godets et la glissière d’air. Le produit fini sera envoyé par la glissière d’air vers les silos à ciment et les particules grossières retourneront au broyeur à boulets. Les gaz d’échappement de l’usine seront purifiés dans le filtre à manches et émis dans l’atmosphère.
5.13 Stockage du ciment
Quatre silos à ciment d’un diamètre de 15 m et d’une capacité de stockage de 20 000 t. Le ciment de la cimenterie est transporté jusqu’au sommet du silo par élévateur. Le ciment dans le silo est passé de la glissière au bac du milieu, le ciment déchargé du bac du milieu a été transporté du véhicule de vrac de ciment (3×150 t/h), un autre transporté au packer de ciment par glissière d’air.
5.14 Emballage en ciment
Deux ensembles d’emballeurs de ciment (emballeur rotatif à 8 becs, 100 t/h) seront utilisés pour l’emballage du ciment.
La poussière causée par l’emballage est collectée par des filtres à manches et envoyée à l’élévateur à godets avant l’emballeur par un convoyeur à vis tandis que l’air vicié s’écoule à travers un ventilateur.
5.15 Broyage du charbon
Le système de broyage du charbon adoptera un broyeur à boulets. Lorsque l’humidité du charbon brut est de ≤10 %), l’humidité du produit est de ≤1 % et la taille du charbon brut est de ≤25 mm, la finesse du produit est de 80m de résidu de tamis ≤10 %, puis la sortie de l’ensemble du système est de 18t / h.
5.16 RCC et laboratoire central. Dans le CCR, l’opération et le contrôle de routine du processus seront exécutés, et dans le laboratoire central, le contrôle de la qualité et les tests des matières premières, du carburant, du produit fini et du produit semi-fini seront effectués.
5.17 Station de compression d’air
Une station de compression d’air sera installée, 5 ensembles de compresseur d’air à vis dans tout 23m3 / min comme déplacement et pression est de 0,8Mpa, fournissant l’air comprimé sec, sans huile et sans eau pour les consommateurs dans la ligne de production.
Technica
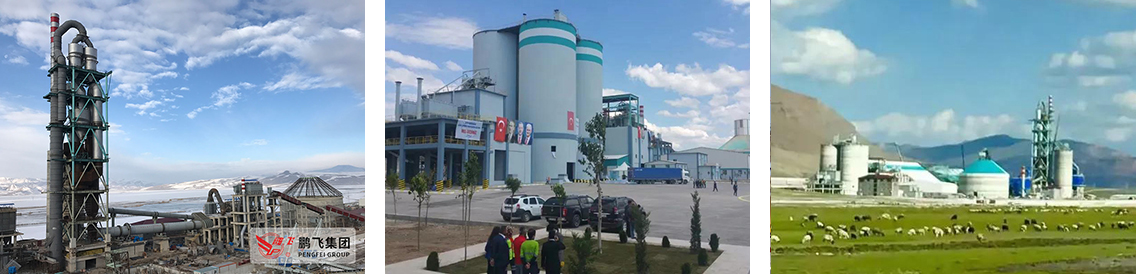
Non. | Département | Performance technique | Capacité (t/h) | Qté | Circulation annuelle Taux( %) |
1 | Broyage du calcaire | Alimentateur de plaques à usage intensif taille :B2000×9018mm Taille des grains : ≤1000mm puissance : 45kW (V · F) |
550 | 1 | 17.6 |
Concasseur à marteaux à un étage taille :PPC-2018 Taille du produit : ≤65mm(90 %) puissance :710 kW |
550 | 1 | 17.6 | ||
2 | Stockage de pré-mélange de calcaire | Gerbeur latéral en porte-à-faux Angle de repos du matériau : 38° Capacité : 500t / h récupérateur de racleur Capacité :300 t/h puissance : ~125kW |
600 300 | 1 1 | 17.6 32 |
3 | Broyage de l’argile | broyeur d’argile Taille maximale : <400mm Taille de décharge (résidu 10 %) : ≤50 mm Humidité du matériau : ≤20 % puissance : 2×37kW |
80 | 1 | 20 |
4 | Matériel auxiliaire et prémélange de charbon | Gerbeur latéral en porte-à-faux Angle de repos du matériau : 38° Capacité : 250t / h racleur récupérateur Capacité :150 t/h puissance : ~125kW |
250 150 | 1 2 | 19 32 |
4 | Broyeur de matières premières | Moulin vertical Humidité de l’alimentation : ≤10 % Granulométrie d’alimentation :≤75mm Humidité de refoulement :≤1 % Finesse de décharge : ≤14 %(résidu de 0,09 mm) puissance du moteur : 2000kW |
210 | 1 | 70 |
Séparateur Type: puissance du moteur : 110kW |
1 | 70 | |||
Ventilateur de circulation Capacité : 450000m3/h pression : 10000Pa puissance du moteur : 1800kW |
1 | 70 | |||
5 | Entrée du four | Ventilateur haute température Capacité :480000m3/h pression : 7500Pa puissance du moteur : 1400kW |
104.2 | 1 | 85.00 |
Système de pulvérisation d’eau 8000x30000 Volume : 480000m3/h Température de l’air d’entrée : 350 °C (max. 450 °C) Température de l’air de sortie : <150°C Volume de pulvérisation d’eau : 2,0 ~ 20m3 / h |
1 | 85.00 | |||
Filtre à manches Capacité :480000m3/h Densité de sortie : ≤30mg/Nm3 |
1 | 85.00 | |||
ventilateur pour gaz résiduaires Capacité :480000m3/h pression : 4000Pa puissance du moteur : 800kW |
1 | 85.00 | |||
Système de préchauffage et de pré-calcination à 5 cyclones : RF5/2000 C1:2-Φ4600mm C2:1-Φ6500mm C3:1-Φ6500mm C4:1-Φ6800mm C5:1-Φ6800mm calcinateur :Φ5050x30000 mm Capacité :2500 t/j |
1 | 85.00 | |||
6 | Four | four rotatif Type : Φ4.0×60m Pente : 4 % Rev 0.39-4.10r/min puissance du moteur : 355kW (DC) |
104.2 | 1 | 85.00 |
7 | Refroidissement du clinker | refroidisseur de grille : faisceau d’air de troisième génération Type :LBT2500 Surface utile de la grille :65m2 température de décharge : température ambiante+65°C Capacité : 2500 ~ 3000 t / j |
104.2 | 1 | 85.00 |
8 | Traitement des effluents gazeux à la sortie du four | Échangeur Volume de traitement : 300000m3/h température d’entrée : 250°C (max.450°C) température de sortie : 130 °C (max. 180 °C) |
1 | 85.00 | |
EP Capacité :300000m3/h Densité de sortie : ≤30mg/Nm3 |
1 | 85.00 | |||
Souffleur pour gaz résiduaires Capacité :300000m3/h pression : 2300Pa puissance du moteur :355kW |
1 | 85.00 | |||
9 | broyage du ciment | Cimenterie Type : T3.8×13m Taille du grain d’alimentation :≤25mm Finesse du produit : Surface spécifique : 3400cm2/g puissance du moteur : 2500kW |
70~75 | 2 | 75.00 |
séparateur N2000 type O-sepa Capacité d’alimentation maximale : 300t / h Sortie du produit : 60 ~ 100t / h |
2 | 75.00 | |||
Filtre à manches Capacité : 120000m3/h Densité de sortie : ≤30mg/Nm3 |
2 | 75.00 | |||
Ventilateur pour gaz résiduaires Capacité : 12000m3/h Pression : 8000Pa |
2 | 75.00 | |||
10 | Gypse écrasant |
Concasseur à mâchoires Type : PEX250×1000 granulométrie maximale : <210 mm Granulométrie de décharge :≤25 mm puissance du moteur : 37 kW |
20 | 1 | 20 |
11 | emballage de ciment et Chargement en vrac |
Machine d’emballage rotative à huit bouches Précision de pesage : +0,5 kg -0,2 kg |
100 | 2 | |
Système de chargement en vrac | 150 | 3 | |||
12 | Station de compression d’air | compresseur d’air à vis Capacité de décharge : 23m3/min pression de refoulement : 0.8MPa puissance du moteur : 132kW |
5 | 85.00 | |
Broyage du charbon | Broyeur à boulets Type : 3×(7+2) m Humidité des aliments : ≤10 % Granulométrie : ≤25 mm Humidité de refoulement : ≤1 % Finesse de décharge : 8-10 % (résidu de 0,08 mm) Puissance du moteur hôte : 630 kW |
20 ~ 22 | 1 | 68 | |
Séparateur dynamique de broyeur à charbon Capacité : 16 ~ 20t / h Volume : 36000m3 / h ~ 50000m3 / h Finesse : ≤6 % (résidu de 0,08 mm) Puissance du moteur : 22kW |
1 | 68 | |||
Filtre à manches Capacité : 55000m3/h Densité de sortie : ≤30mg/Nm3 |
1 | 68 |