Ligne de production de ciment avec une production annuelle de 1,2 million de tonnes
Le projet de ligne de production de ciment EPC de Pengfei comprend la conception du processus, la fourniture d’équipements (y compris les pièces mécaniques et électriques), le génie civil, l’installation et la mise en service, l’exploitation d’essai, l’atteinte de la norme de production et la livraison finale et d’autres services. L’équipement mécanique comprend le concassage et le transport du calcaire, le concassage de l’argile, le concassage du charbon brut, le charbon brut et la cour de pré-homogénéisation des matières premières auxiliaires, la station de dosage des matières premières, le broyage des matières premières et le traitement des gaz résiduaires, le silo d’homogénéisation des matières premières et l’alimentation des matières premières dans le four, la queue du four de cuisson, le tuyau d’air moyen et tertiaire du four de cuisson, la tête du four de cuisson.
Introduction
Le projet de ligne de production de ciment EPC de Pengfei comprend la conception du processus, la fourniture d’équipements (y compris les pièces mécaniques et électriques), le génie civil, l’installation et la mise en service, l’exploitation d’essai, l’atteinte de la norme de production et la livraison finale et d’autres services. L’équipement mécanique comprend le concassage et le transport du calcaire, le concassage de l’argile, le broyage du charbon brut, le charbon brut et la cour de pré-homogénéisation des matières premières auxiliaires, la station de dosage des matières premières, le broyage des matières premières et le traitement des gaz résiduaires, le silo d’homogénéisation des matières premières et l’alimentation des matières premières dans le four, la queue du four de cuisson, le tuyau d’air moyen et tertiaire du four de cuisson, la tête du four de cuisson, le transport de clinker, Stockage et convoyage de clinker, préparation et dosage du charbon pulvérisé, station de dosage de ciment et clinker en vrac, gypse, broyage et convoyage de mélange, broyage et convoyage de ciment, stockage et convoyage de ciment, emballage de ciment, chargement de ciment en sac, camion de ciment en vrac, atelier de réparation de machines et entrepôt de matériaux complets.Paramètre de processus
(1)Sortie de clinker : ≥3300 t / j ;(2) Consommation de chaleur de combustion du clinker
(3) Consommation d’énergie complète du clinker
(4) Consommation d’énergie complète du ciment
(5) 20 jours de résistance du clinker
(6) contenu évacuant la poussière
Méthode de fabrication
Dans la production de ciment, le calcaire et l’argile sont utilisés comme matières premières principales, qui sont broyées, proportionnées et broyées en matières premières par presse à rouleau, puis introduites dans le four rotatif à ciment pour calciner les matériaux matures, puis le clinker est ajouté avec une quantité appropriée de gypse, mélangé à des matériaux mélangés ou à des additifs, puis laminé et broyé en ciment par presse à rouleaux et broyeur à ciment, puis transporté hors de l’usine par une machine d’emballage ou une machine en vrac. L’équipement de production de ciment adopte généralement le processus de production de ciment sec. La méthode consistant à sécher les matières premières en même temps et à les broyer en poudre de farine brute et à les introduire dans un four rotatif sec pour les calciner en clinker. Le principal avantage de la production à sec est la faible consommation de chaleur.Description du processus
Le calcaire est versé dans la trémie par le camion à benne basculante de broyage du calcaire. Après avoir été broyé par le concasseur à marteaux, il est envoyé au chantier de pré-homogénéisation du calcaire par le convoyeur à bande. L’empileur en porte-à-faux est utilisé pour l’empilage et la récupération en couches. Le calcaire retiré est envoyé dans le bac de dosage du calcaire de la station de dosage des matières premières par convoyeur à bande. Un déferriseur électromagnétique est disposé sur le convoyeur à bande d’entreposage pour éliminer les éventuelles pièces en fer dans le calcaire. La tête du convoyeur à bande est équipée d’un détecteur de métaux pour détecter s’il reste des pièces en fer dans les matières premières, afin d’éviter d’endommager la presse à rouleaux de broyage des matières premières. La station de dosage des matières premières est équipée de bacs de dosage de calcaire, d’argile et d’autres bacs. Le fond de chaque bac de dosage est équipé d’un alimentateur à plaques et d’un alimentateur quantitatif. Quatre types de matières premières sont déchargés par leurs doseurs quantitatifs respectifs en fonction de la proportion requise par le dosage. Les matériaux sont introduits dans le petit bac de la presse à rouleaux de broyage des matières premières par l’intermédiaire du convoyeur à bande.Le système de presse à rouleaux est adopté pour le broyage des matières premières, et les gaz résiduaires à haute température évacués de la queue du four sont utilisés comme source de chaleur de séchage. Après avoir été extrudés par une presse à rouleaux, les matériaux sont séchés et calibrés par un concentrateur de poudre de type V. Une fois que la poudre fine est sélectionnée par un concentrateur de poudre à haut rendement, une partie de la poudre fine est envoyée dans le silo d’homogénéisation de la farine crue par une goulotte de transport d’air et un élévateur à godets.
Le moulin à charbon est situé à l’extrémité du four. Une partie des gaz résiduaires de l’extrémité du four est utilisée comme source de chaleur de séchage du charbon brut après avoir été collectée par le cyclone. Après l’humidification et le refroidissement du gaz de queue de four par la tour d’humidification, il entrera directement dans le dépoussiéreur électrique à la queue du four. Le volume de pulvérisation d’eau de la tour d’humidification sera automatiquement contrôlé en fonction de la température des gaz résiduaires à la sortie de la tour d’humidification, de sorte que la température des gaz résiduaires se situe dans la plage autorisée du dépoussiéreur électrique à la queue du four. Les gaz résiduaires purifiés du dépoussiéreur seront évacués dans l’atmosphère par un ventilateur d’extraction. Les cendres du four collectées par la tour d’humidification sont envoyées au système d’alimentation du four ou au silo d’homogénéisation de la farine crue à travers l’équipement de convoyage. Un silo continu d’homogénéisation de la farine crue est mis en place. La farine crue dans le silo est évacuée vers la chambre de mélange à partir de la zone annulaire environnante après avoir été gonflée alternativement et uniformément dans la chambre de mélange. Le gonflage inférieur requis est fourni par le ventilateur de racines configuré. Après avoir été mesurée, la farine crue homogénéisée est acheminée par air vers l’auge inclinée et l’élévateur à godets, puis acheminée vers les deux orifices d’alimentation du préchauffeur à double série respectivement par la vanne de distribution et la vanne de sas.
L’atelier de cuisson est composé d’un préchauffeur à suspension à double série à cinq étages, d’un four de décomposition, d’un four rotatif, d’un refroidisseur à grille et d’un système de dépoussiérage correspondant, avec une production quotidienne de 3300 t de clinker. La matière première introduite dans le préchauffeur est préchauffée par le préchauffeur et décomposée dans le four en décomposition, puis introduite dans le four pour la calcination ; Le clinker à haute température sorti du four est refroidi dans le refroidisseur à grille, et le gros clinker est écrasé par le concasseur, puis collecté avec le petit clinker qui s’est échappé dans la chambre à air, puis envoyé à l’entrepôt de clinker pour être stocké par le convoyeur à godets à chaîne de clinker. En plus de fournir de l’air secondaire et de l’air tertiaire à haute température au four et au four de décomposition respectivement, l’air chaud à travers le lit de clinker est évacué dans l’atmosphère par le ventilateur d’extraction après avoir été purifié par le dépoussiéreur électrique. Une fois que le clinker est déchargé par le dispositif de déchargement au fond du silo, il est envoyé à la station du camion de vrac par le convoyeur à bande, et le clinker en vrac est directement chargé par la tête de gonflant sans poussière au fond de chaque silo.
Le système de pulvérisation est adopté pour la préparation du charbon pulvérisé, et les gaz résiduaires à haute température déchargés de la queue du four sont utilisés comme source de chaleur de séchage. Le charbon brut est introduit dans le broyeur à charbon par l’alimentateur quantitatif situé sous la trémie à charbon brut pour le séchage et le broyage. Le charbon pulvérisé sortant de l’usine entre dans le dépoussiéreur de type sac avec le flux d’air. Le charbon pulvérisé qualifié est collecté et envoyé à la trémie à charbon pulvérisé avec le capteur de charge par le convoyeur à vis. Le charbon pulvérisé est dosé et envoyé au brûleur à la tête du four et au four en décomposition à la queue du four pour la combustion. La poussière contenant du gaz est purifiée par le dépoussiéreur à sac antistatique, puis évacuée dans l’atmosphère par le ventilateur d’extraction. La trémie à charbon et le dépoussiéreur à sac sont équipés d’un détecteur de CO et d’une soupape antidéflagrante. Un laboratoire central est mis en place dans l’ensemble de l’usine pour être chargé de l’inspection du combustible brut, des produits semi-finis et des produits finis ; Et une station de compression d’air est mise en place pour fournir de l’air comprimé pour la production de l’ensemble de l’installation.
Le clinker, le gypse et les additifs du système de dosage du ciment sont dosés par le doseur quantitatif situé au fond du silo, puis introduits dans le système de broyage du ciment pour le broyage par le convoyeur à bande et l’élévateur. Le système de broyage du ciment est composé de deux ensembles de presse à rouleaux pfg160-140 Φ 3,2 × broyeur à boulets de 13 m.
Le ciment est stocké dans un entrepôt de 2 à φ 18m de diamètre. Le ciment déchargé de l’entrepôt est déchargé dans le bac de dosage du ciment par l’orifice de déchargement situé au fond de chaque bac. La trémie doseuse de ciment est équipée d’un capteur de charge et d’un dispositif de gonflage. Il y a quatre orifices de décharge sous le bac, et chaque orifice de décharge est équipé d’une soupape de régulation de débit et d’un débitmètre. Le ciment dosé est envoyé au système d’emballage du ciment par la goulotte de transport aérien, et les deux autres sont utilisés pour le chargement en vrac au fond du bac. La capacité nominale du système en vrac est de 150t / H.
Technique
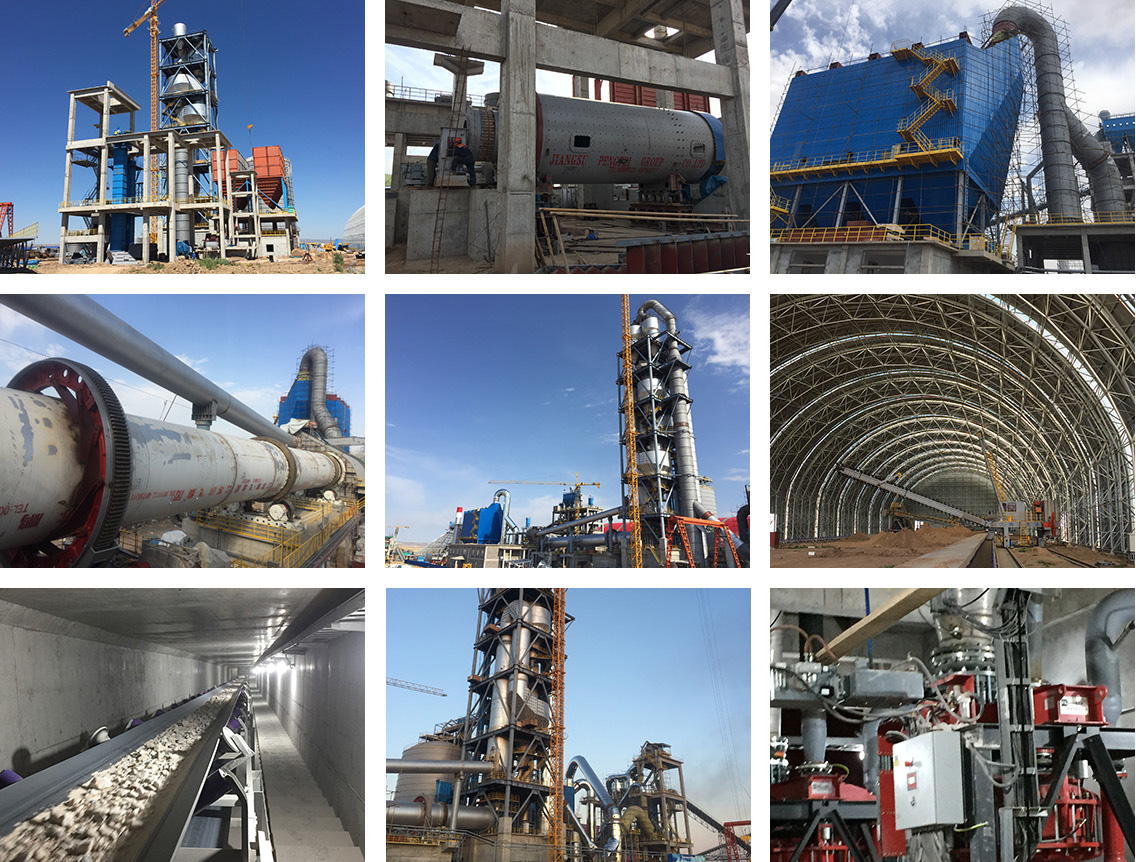
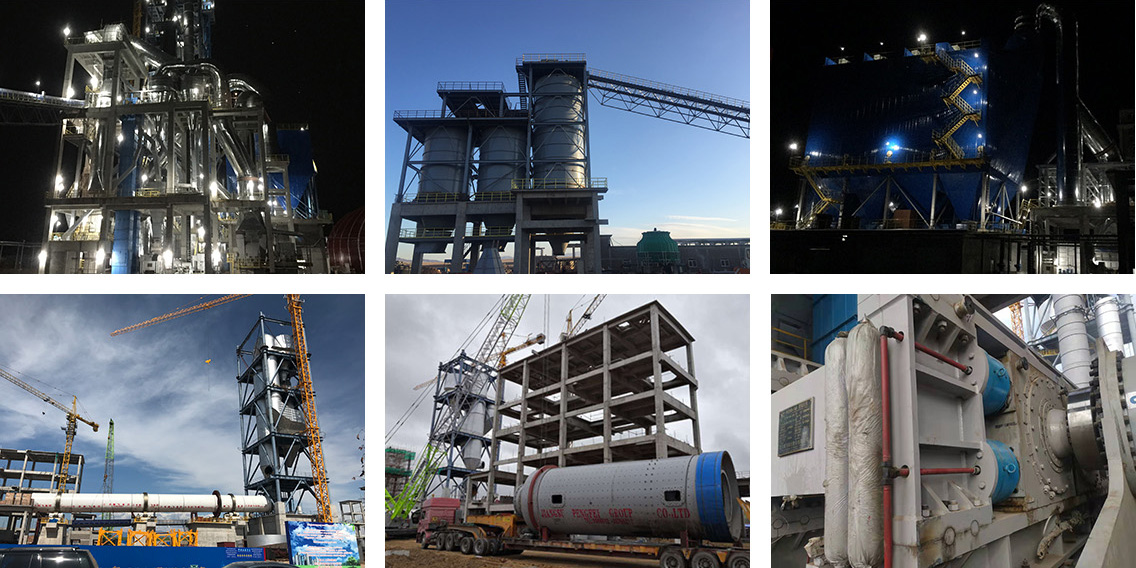
Numéro d’article | Non. | Nom | Spécification | Unité | Quantité |
02 | 01 | Mangeoire à tablier | Modèle : B2200×10000mm | poser | 1 |
12 | 10 | Concasseur à mâchoires | Modèle :TPE100 | poser | 1 |
41 | 10 | Presse à rouleaux | Modèle : PFG180-120 gauche installé | 台 | 1 |
Diamètre du rouleau d’extrusion : 1800 mm | |||||
Largeur du rouleau d’extrusion : 1200 mm | |||||
Passage à travers : 600 ~ 850t / h | |||||
Granularité d’alimentation : ≤50mm | |||||
Sortie : 260t / h | |||||
56 | 01 | Four rotatif | Taille : Φ4.3×60m | 台 | 1 |
Sortie ::3300t/d | |||||
Non. Du dispositif de rouleau de support : 3 | |||||
Consommation d’eau de chaque rouleau de support : 4m3/h | |||||
Inclinaison : 4 % | |||||
Vitesse de rotation auxiliaire : 7,93 r / h | |||||
57 | 01 | Hotte de four | Taille : Φ4.3x60m hotte de four rotatif | 台 | 1 |
57 | 02 | Dispositif de combustion de poudre de charbon | Pulvérisation de poudre de charbon : 7,5 t / h / h / max : 10 t / h | 台 | 1 |
Hauteur centrale du tuyau de pulvérisation de charbon : 1500mm | |||||
57 | 08 | Glacière à grille | Modèle :SCLW4-8X12-RC | 台 | 1 |
Capacité frigorifique :Capacité nominale 3300t/d Max. Capacité 3600t/d | |||||
57 | 17 | Filtre EP | Modèle : 29/12.5 / 4 * 9 / 0.45 | 台 | 1 |
73 | 04 | Moulin à charbon à balayage d’air | Taille : Φ3.4×(6.5 + 2.5) m | 台 | 1 |
Capacité : 30t / h | |||||
Granularité d’alimentation :≤25mm | |||||
Finesse du produit fini : écran à trou de 0,08 mm, résidu≤3 % | |||||
84 | 31~32 | Broyeur de ciment | Taille : Φ3.2x13m | 台 | 2 |
Capacité : 110t / h | |||||
Granularité d’alimentation ≤2mm | |||||
Teneur en humidité d’alimentation :≤0.5 % | |||||
Blaine : 3200±100cm2/g |